Як обробляються високоточні деталі
2023-09-22
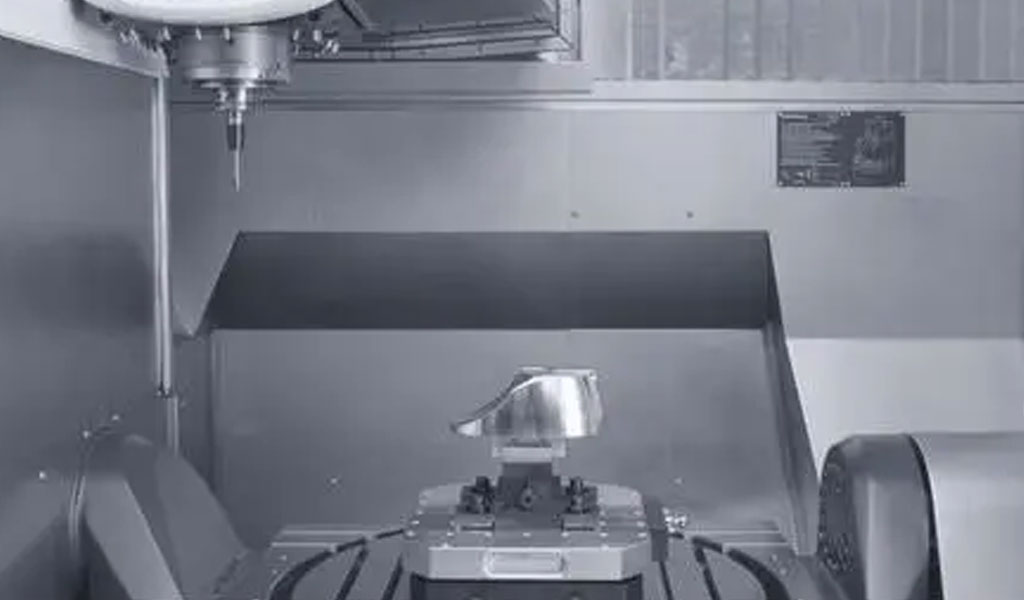
Розуміння точної обробки
Точна обробка є наріжним каменем сучасного виробництва, відповідального за виготовлення складних і точних компонентів, які використовуються в широкому діапазоні галузей. Щоб повністю зрозуміти його значення, давайте дослідимо основні концепції прецизійної обробки, її життєво важливу роль у різних секторах та історичну подорож, яка привела до її нинішнього рівня досконалості.A. Що таке точна обробка?
Точна механічна обробка відноситься до набору виробничих процесів, які видаляють матеріал із заготовки з високим ступенем точності та контролю, в результаті чого отримують тонко оброблені компоненти з жорсткими допусками. Цей процес перетворює сировину, таку як метали, пластмаси чи кераміку, на точні деталі, які відповідають суворим специфікаціям. Основні характеристики точної обробки включають:- Точність: Точна механічна обробка гарантує, що кінцевий продукт точно відповідає запланованому дизайну з мінімальними відхиленнями.
- Жорсткі допуски: Це дозволяє виготовляти деталі з надзвичайно жорсткими допусками, тобто готові компоненти точно відповідають заданим розмірам.
- Чудова обробка поверхні: Точна обробка забезпечує виняткову обробку поверхні, часто усуваючи потребу в додаткових процесах обробки.
- Комплексні геометрії: Він може створювати складні форми, контури та елементи, що робить його незамінним у виробництві компонентів зі складною конструкцією.
- Повторюваність: Точність процес механічної обробкиВони мають високу повторюваність, забезпечуючи незмінну якість багатьох деталей.
- Гнучкість: Його можна застосовувати до широкого діапазону матеріалів, що робить його придатним для різноманітних галузей промисловості.
B. Важливість точної обробки
Точна обробка має величезне значення в кількох важливих галузях, впливаючи на різні аспекти нашого повсякденного життя. Ось кілька переконливих причин його важливості:- Аерокосмічна промисловість: В аерокосмічному секторі точна механічна обробка є незамінною для виготовлення компонентів, які витримують екстремальні умови. Авіаційні двигуни, посадка передача, а структурні елементи покладаються на прецизійні деталі для безпеки та продуктивності.
- Медичні прилади: Медичні пристрої, такі як хірургічні інструменти, протези та імплантовані пристрої, вимагають точної обробки для забезпечення біосумісності, точності та безпеки пацієнтів.
- Автомобільний сектор: Точні деталі мають важливе значення для автомобільної промисловості для забезпечення надійності та ефективності транспортних засобів. Такі компоненти, як деталі двигуна, системи трансмісії та гальмівні механізми, залежать від точної механічної обробки.
- Електроніка та напівпровідники: Точна обробка є ключовою у виробництві мікроелектронних компонентів і напівпровідникових пристроїв, де мінімальні допуски є обов’язковими для функціональності.
- Енергетичний сектор: Енергетична промисловість покладається на прецизійну механічну обробку для виробництва критичних деталей, які використовуються у виробництві електроенергії, включаючи турбіни, генератори та компоненти трансмісії.
- Виготовлення інструментів і штампів: Точна обробка має вирішальне значення у виробництві інструментів і штампів, які, у свою чергу, використовуються для створення незліченної кількості інших виробів.
- Побутова електроніка: Виробництво смартфонів, ноутбуків та іншої споживчої електроніки виграє від точної обробки для забезпечення елегантного дизайну та оптимальної функціональності.
- Дослідження та розвиток: Дослідники та вчені покладаються на прецизійні компоненти для експериментів, прототипів і лабораторного обладнання.
C. Історична перспектива
Подорож до точної обробки бере свій початок із стародавніх цивілізацій, де вправні ремісники використовували елементарні інструменти для формування матеріалів. Однак точність, досягнута в ті часи, була обмеженою порівняно з сучасними стандартами.- Рання точна обробка: промислова революція 18-го та 19-го століть ознаменувала переломний період у розвитку точної обробки. Винахід верстатів, таких як токарні та фрезерні верстати, зробив революцію у виробництві, забезпечивши більшу точність і послідовність.
- Друга світова війна: Прецизійна обробка зіграла ключову роль у Другій світовій війні, оскільки вона була важливою для виробництва військового обладнання з необхідною точністю та однорідністю. Ця епоха стала свідком прогресу в техніці обробки та появи нових матеріалів.
- Післявоєнні досягнення: У післявоєнний період спостерігався сплеск технологічних інновацій, включаючи використання верстатів з числовим програмним керуванням (ЧПК). Обробка з ЧПУ дає змогу виконувати автоматизовані та високоточні операції, відкриваючи нову еру виробництва.
- Цифрова ера: Інтеграція комп’ютерів і програмного забезпечення в процеси обробки ще більше підвищила точність обробки. Сучасні верстати з ЧПК можуть виконувати складні операції з неперевершеною точністю, що робить їх незамінними в сучасному виробничому ландшафті.
Матеріали та їх значення
Матеріали є основою точної обробки, і вибір правильного матеріалу відіграє ключову роль у виробництві високоточних деталей. У цьому розділі ми заглибимося в важливість вибору відповідних матеріалів, зрозуміємо важливість властивостей матеріалу та дослідимо різні фактори, які впливають на оброблюваність.A. Відбір матеріалів
Вибір матеріалів для точної обробки є критичним рішенням, яке безпосередньо впливає на продуктивність, довговічність і функціональність кінцевого продукту. При виборі матеріалів виробники повинні враховувати кілька факторів:- Придатність матеріалу: Матеріал повинен відповідати призначенню. Різні галузі промисловості та застосування мають різні вимоги, такі як термостійкість, стійкість до корозії та електропровідність.
- Механічні властивості: механічні властивості, такі як міцність на розрив, твердість і пластичність, є вирішальними. Наприклад, в аерокосмічній галузі матеріали з високою міцністю на розрив є кращими для конструктивних компонентів.
- Теплові властивості: Для деяких застосувань потрібні матеріали з відмінною теплопровідністю або стійкістю до високих температур. Це особливо важливо в таких галузях, як виробництво електроенергії та електроніка.
- Стійкість до корозії: У середовищах, де корозія викликає занепокоєння, перевагу надають матеріалам з високою стійкістю до корозії, таким як нержавіюча сталь або титан.
- Розгляд ваги: Такі галузі, як автомобільна та авіакосмічна промисловість, часто віддають перевагу легким матеріалам, таким як алюміній або композити з вуглецевого волокна, щоб зменшити споживання палива та підвищити продуктивність.
- Обмеження вартості: Вартість є важливим фактором при виборі матеріалу. Високоефективні матеріали можуть бути дорогими, тому виробники повинні знайти баланс між продуктивністю та економічною ефективністю.
- Відповідність нормативам: У таких галузях, як охорона здоров’я, матеріали мають відповідати суворим нормативним стандартам біосумісності та безпеки.
- доступність: Доступність матеріалів та їх джерел також впливає на вибір. Доступність деяких спеціальних сплавів або композитів може бути обмежена.
B. Властивості матеріалу
Розуміння властивостей матеріалів має вирішальне значення для точної обробки. Ось деякі основні властивості матеріалу та їх значення:- Міцність на розрив: Міцність на розрив вимірює здатність матеріалу витримувати силу розтягування без руйнування. Він важливий для структурних компонентів і деталей, які піддаються механічним навантаженням.
- Твердість: Твердість вказує на стійкість матеріалу до деформації та зношування. Тверді матеріали підходять для ріжучих інструментів, тоді як м’які матеріали можуть бути кращими для певних застосувань, наприклад ущільнень.
- Пластичність: Пластичність означає здатність матеріалу деформуватися без руйнування під дією напруги розтягування. Пластичні матеріали легше формувати, але вони можуть бути непридатними для застосування, де потрібна жорсткість.
- Теплопровідність: Матеріали з високою теплопровідністю ефективно розсіюють тепло. Ця властивість життєво важлива в програмах, де контроль температури є критичним.
- Електропровідність: Електропровідність має важливе значення в електроніці та електричних компонентах, де матеріали мають сприяти проходженню електроенергії.
- Магнітні властивості: Магнітні властивості важливі в таких галузях промисловості, як електромагнетика та електроніка, де матеріали можуть бути феромагнітними або немагнітними.
- Хімічна стійкість: Матеріали мають бути стійкими до хімічної корозії в середовищах, де вони піддаються впливу кислот, лугів або інших корозійних речовин.
C. Фактори оброблюваності
Оброблюваність означає легкість, з якою матеріал можна обробляти, різати або формувати. На нього впливають різні фактори, серед яких:- Твердість матеріалу: М’які матеріали, як правило, легше обробляти, тоді як для більш твердих матеріалів можуть знадобитися спеціальні інструменти та методи.
- Формування стружки: Утворення та видалення стружки під час механічної обробки впливають на ефективність процесу та якість поверхні.
- Знос інструменту: Різні матеріали можуть спричиняти різний ступінь зносу інструменту, впливаючи на швидкість обробки та вартість.
- Охолоджуюча рідина та мастило: Правильна охолоджуюча рідина та змащення мають важливе значення для зменшення тертя, тепла та зносу інструменту під час обробки.
- Швидкість різання: швидкість, з якою ріжучий інструмент рухається крізь матеріал, впливає як на продуктивність, так і на якість обробленої поверхні.
- Матеріал інструменту: Вибір матеріалу ріжучого інструменту, такого як твердий сплав або швидкорізальна сталь, залежить від матеріалу, який обробляється.
- Параметри різання: Регулювання параметрів різання, таких як швидкість подачі та глибина різання, може оптимізувати процес обробки для конкретних матеріалів.
Верстати для точної обробки
Верстати є серцем прецизійної обробки, що дозволяє перетворювати вихідні матеріали у високоточні деталі. У цьому розділі ми розглянемо чотири ключові типи верстатів, які використовуються для точної обробки: обробні центри з ЧПК, токарні верстати, шліфувальні верстати та електроерозійна обробка (EDM). Кожна з цих машин відіграє унікальну роль у виробництві точних компонентів.A. Обробні центри з ЧПК
Обробні центри з ЧПУ (комп’ютерне числове керування) є універсальними та широко використовуються в прецизійній обробці. Це автоматизовані системи, які з надзвичайною точністю контролюють рух ріжучих інструментів і заготовок. Ось огляд обробних центрів з ЧПК та їх значення:- Гнучкість: Обробні центри з ЧПК можуть виконувати різноманітні операції обробки, включаючи фрезерування, свердління та нарізування різьби. Ця універсальність дозволяє виготовляти складні деталі з багатьма функціями.
- Висока точність: Комп’ютеризоване керування верстатами з ЧПК забезпечує точне позиціонування інструменту та стабільні результати, що робить їх ідеальними для деталей із жорсткими допусками.
- Автоматизація: Обробні центри з ЧПК можуть працювати безперервно з мінімальним втручанням людини. Така автоматизація підвищує ефективність і знижує ризик помилок.
- Комплексні геометрії: вони чудово підходять для обробки складних форм і контурів, що робить їх придатними для таких галузей промисловості, як авіакосмічна промисловість, де складні компоненти поширені.
- Повторювані результати: Верстати з ЧПК забезпечують чудову повторюваність, гарантуючи, що кожна виготовлена деталь точно відповідає специфікаціям конструкції.
- Скорочений час налаштування: обробні центри з ЧПК можна запрограмувати на швидке перемикання між різними завданнями, мінімізуючи час налаштування та підвищуючи ефективність виробництва.
B. Токарні верстати
Токарні верстати використовуються для створення циліндричних деталей шляхом обертання заготовки, в той час як ріжучий інструмент видаляє матеріал з її зовнішньої поверхні. Вони необхідні для виробництва валs, штифти та інші компоненти з обертальною симетрією. Основні моменти щодо токарних верстатів включають:- Циліндричні деталі: Токарні верстати спеціалізуються на виготовленні циліндричних або трубчастих деталей, у тому числі з різьбою або складними канавками.
- Високі швидкості: Вони працюють на високих швидкостях, що робить їх придатними для деталей, які потребують гладкої та точної обробки.
- Одноосьова операція: Більшість токарних верстатів є одноосьовими, зосередженими на формуванні зовнішньої поверхні заготовки.
- Ефективний для масового виробництва: Токарна обробка є високоефективною для масового виробництва деталей з мінімальними відходами.
- Токарні верстати: Токарні верстати з ручним керуванням і ЧПК – це широко використовувані токарні верстати, які пропонують ряд можливостей.
C. Шліфувальні машини
Шліфувальні верстати призначені для точної обробки поверхонь і формування твердих або абразивних матеріалів. Вони мають вирішальне значення для досягнення надзвичайно жорстких допусків і чудової обробки поверхні. Ось чому шліфувальні машини важливі:- Точність мікронного рівня: Шліфувальні машини можуть досягати мікронної точності, що робить їх необхідними для застосувань, які вимагають найвищого рівня точності.
- Видалення матеріалу: Вони видаляють матеріал шляхом стирання, дозволяючи виправити недоліки поверхні та досягти виняткової гладкості.
- Заточування інструменту та фрези: Крім поверхневого шліфування, існують спеціалізовані шліфувальні верстати для заточування ріжучих інструментів і виготовлення точних профілів.
- Різноманітність методів подрібнення: Різні типи шліфувальних верстатів, включаючи плоскошліфувальні, циліндричні та безцентрові шліфувальні машини, задовольняють різні потреби обробки.
- Загартовані матеріали: Шліфування особливо підходить для загартованих матеріалів, таких як інструментальна сталь і кераміка, де традиційні методи обробки можуть бути неефективними.
D. EDM (електророзрядна обробка)
EDM, або електроерозійна обробка, — це нетрадиційний процес обробки, який використовує електричні розряди для формування матеріалів. Він ідеально підходить для створення складних і делікатних деталей, де традиційні ріжучі інструменти можуть пошкодити. Основні аспекти EDM включають:- Немає фізичного контакту: EDM не передбачає прямого фізичного контакту між інструментом і деталлю, мінімізуючи ризик зносу інструменту та пошкодження крихких матеріалів.
- Висока точність: Він може досягти високої точності та якості обробки поверхні навіть з виключно твердими матеріалами.
- Електроерозія дроту та Електроерозія грузила: Є два основних типи машин EDM: різання дроту EDM, який використовує дротяний електрод, і грузильний EDM, який використовує фасонний електрод.
- Складні форми: EDM може виготовляти складні форми, такі як штампи та прес-форми, зі складними деталями та тонкими деталями.
- Зона теплового впливу: Оскільки EDM не генерує тепло на деталі, він підходить для термочутливих матеріалів, таких як аерокосмічні сплави.
- Повільний процес: EDM є відносно повільним у порівнянні з іншими методами обробки, що робить його найкращим для виконання невеликих обсягів високоточних завдань.
Ріжучі інструменти та оснастка
Ріжучі інструменти знаходяться на передньому краї точної обробки, слугуючи інструментами, які формують і перетворюють вихідні матеріали на високоточні деталі. У цьому розділі ми вивчимо різні типи різальних інструментів, важливість покриття інструментів і фактори, що впливають на термін служби інструменту та знос.А. Види ріжучих інструментів
Точна обробка базується на різноманітному діапазоні ріжучих інструментів, кожен з яких призначений для конкретних завдань і матеріалів. Вибір ріжучого інструменту значною мірою впливає на ефективність і точність процесу обробки. Ось кілька поширених типів ріжучих інструментів:- Кінцеві фрези: Кінцеві фрези — це універсальні інструменти, які використовуються для фрезерування. Вони мають кілька ріжучих кромок і можуть видаляти матеріал із заготовки різними способами, включаючи облицювання, обробку контурів і прорізання.
- Свердла: Свердла призначені для створення отворів у заготовках. Вони бувають різних форм, включаючи спіральні свердла, центральні свердла та змінні свердла.
- Токарні вставки: вони використовуються в токарних верстатах для формування циліндричних деталей. Токарні пластини доступні в різноманітних формах і матеріалах для різних застосувань.
- Фрези: Фрези бувають різних форм, наприклад торцеві фрези, кульові млини та фрези для різання пазів, і використовуються у фрезерних верстатах для створення різноманітних деталей на заготовці.
- Розвідники: Розвертки використовуються для фінішної обробки та визначення точних розмірів раніше просвердлених отворів. Вони забезпечують гладкі та точні поверхні отворів.
- Мітчики та плашки: Ці ріжучі інструменти використовуються для операцій нарізання різьби. Мітчики створюють внутрішню різьбу, тоді як плашки створюють зовнішню різьбу.
- ШЛИФКРУГ: Шліфувальні круги - це абразивні інструменти, які використовуються для точного поверхневого шліфування. Вони доступні з різними абразивними матеріалами та розмірами зернистості.
- Протяжки: Протяжки — це спеціалізовані інструменти, які використовуються для різання внутрішніх і зовнішніх форм і профілів, таких як шпонкові канавки та шліци.
- Зенкери та зенкери: Ці інструменти використовуються для створення заглиблень або фасок навколо отворів для застібкаs.
- Розточувальні бруски: Свердлильні штанги використовуються в розточувальних операціях для точного розширення наявних отворів.
B. Покриття інструментів
Покриття інструментів — це тонкі шари матеріалу, нанесені на ріжучі інструменти для підвищення їх продуктивності та довговічності. Ці покриття мають ряд переваг:- Зменшене тертя: такі покриття, як нітрид титану (TiN) і карбонітрид титану (TiCN), зменшують тертя між інструментом і деталлю, що забезпечує більш гладке різання та подовжує термін служби інструменту.
- Підвищена твердість: Покриття підвищують твердість поверхні інструменту, роблячи його більш стійким до зношування та подовжуючи термін служби інструменту.
- Покращена термостійкість: Покриття можуть витримувати високі температури, що виникають під час обробки, зменшуючи знос інструменту, пов’язаний із нагріванням, і збільшуючи швидкість різання.
- Властивості проти налипання: Деякі покриття мають антиадгезійні властивості, запобігаючи накопиченню матеріалу на ріжучих кромках інструменту.
- Підвищена змащувальна здатність: Інструменти з покриттям мають покращену змащувальну здатність, зменшуючи потребу в надмірній охолоджувальній рідині та покращуючи відведення стружки.
C. Термін служби та знос інструменту
Розуміння довговічності та зносу інструменту має вирішальне значення для оптимізації процесів обробки та мінімізації виробничих витрат. Термін служби інструменту означає тривалість роботи ріжучого інструменту до того, як його буде потрібно замінити або відновити. Кілька факторів впливають на термін служби та знос інструменту:- Швидкість різання: Вищі швидкості різання можуть призвести до збільшення зносу інструменту через високі температури, що утворюються під час обробки. Правильний вибір швидкості різання має важливе значення для збалансування терміну служби інструменту та продуктивності.
- Швидкість подачі: швидкість, з якою ріжучий інструмент просувається в заготовку, впливає на знос інструменту. Висока подача може прискорити зношування, тоді як менша подача може подовжити термін служби інструменту.
- Глибина різання: Глибина різання впливає на кількість матеріалу, видаленого за один прохід. Більш глибокі різи можуть збільшити знос інструменту, тому оптимізація глибини є критичною.
- Твердість матеріалу: Різання твердих матеріалів може прискорити знос інструменту. Для ефективної обробки твердих матеріалів використовуються спеціальні інструменти та покриття.
- Охолоджуюча рідина та мастило: Правильна охолоджуюча рідина та мастило допомагають розсіювати тепло та зменшувати тертя, подовжуючи термін служби інструменту.
- Матеріал інструменту: Матеріал, з якого виготовлений ріжучий інструмент, впливає на його зносостійкість. Такі матеріали, як карбід і кераміка, забезпечують чудову зносостійкість.
- Геометрія інструменту: Геометрія ріжучого інструменту, включно з переднім кутом, рельєфним кутом і конструкцією стружколома, відіграє значну роль у структурі зношування.
- Матеріал заготовки: Тип матеріалу, що обробляється, впливає на знос інструменту. Абразивні матеріали можуть призвести до швидшого зносу інструменту.
Процеси прецизійної обробки
Процеси прецизійної обробки — це методи, за допомогою яких сировину перетворюють на високоточні деталі з жорсткими допусками та винятковою обробкою поверхні. У цьому розділі ми розглянемо п’ять ключових процесів точної обробки: токарна обробка, фрезерування, свердління, шліфування та електроерозійна обробка (EDM). Кожен із цих процесів служить унікальній меті та використовується на основі конкретних вимог до заготовки.А. Точіння
Токарна обробка — це процес механічної обробки, який в основному використовується для формування циліндричних деталей. Він передбачає обертання заготовки, в той час як одноточковий ріжучий інструмент видаляє матеріал із зовнішньої поверхні. Ось основні аспекти токарної обробки:- Циліндричні деталі: Токарна обробка ідеально підходить для виготовлення циліндричних деталей, таких як вали, штифти та втулки.
- Обертальна симетрія: Він добре підходить для деталей, які вимагають обертальної симетрії, оскільки заготовка обертається на токарному верстаті, а ріжучий інструмент формує її.
- Різні операції: Точіння може виконувати різні операції, включаючи торцювання, точіння (зменшення діаметра), точіння конуса та нарізання різьби.
- Одноточкове різання: один ріжучий інструмент видаляє матеріал безперервним рухом, що забезпечує ефективне видалення матеріалу.
- Токарні верстати: Токарні верстати з ручним керуванням і з ЧПК зазвичай використовуються для токарних операцій.
B. Фрезерування
Фрезерування — це універсальний процес точної обробки, який використовує багатоточкові ріжучі інструменти для видалення матеріалу із заготовки. Він добре підходить для створення широкого діапазону форм і функцій. Основні аспекти фрезерування включають:- Гнучкість: Фрезерування може створювати плоскі поверхні, прорізи, кишені та складні контури. Він використовується як для 2D, так і для 3D обробки.
- Багатоточкове різання: Кілька ріжучих кромок на інструменті взаємодіють із заготівлею одночасно, забезпечуючи ефективне видалення матеріалу.
- Види фрезерування: Фрезерування можна виконувати за допомогою різних типів фрез, включаючи торцеві фрези, торцеві фрези та кульові фрези.
- Обробні центри з ЧПУ: Фрезерні верстати з ЧПК забезпечують точний контроль руху інструменту та широко використовуються в сучасній обробці.
- Високі швидкості: Фрезерування можна виконувати на високих швидкостях, що забезпечує ефективне виробництво.
C. Буріння
Свердління — це точний процес обробки, який використовується для створення отворів у заготовках. Це фундаментальна операція в різних галузях. Основні аспекти буріння включають:- Створення отвору: Свердлильні машини використовують спеціалізовані інструменти, які називаються свердлами, для видалення матеріалу та створення отворів певного діаметру.
- Види свердел: доступні різні типи свердел, у тому числі спіральні, центральні та змінні свердла, кожне з яких розроблено для певних завдань.
- Точність: Точне позиціонування та вирівнювання є важливими під час свердління для забезпечення точного створення отворів.
- Швидкість і швидкість подачі: Такі параметри свердління, як швидкість обертання та швидкість подачі, мають вирішальне значення для досягнення бажаних розмірів отвору.
- Охолоджуюча рідина та мастило: Для розсіювання тепла та зменшення тертя під час свердління використовуються відповідні охолоджувальна рідина та мастило.
D. Шліфування
Шліфування — це точний процес обробки, який використовує абразивні круги для видалення матеріалу та досягнення надзвичайно жорстких допусків і обробки поверхні. Основні аспекти шліфування включають:- Виняткова точність: шліфування може досягти мікронної точності, що робить його ідеальним для застосувань, які вимагають найвищої точності.
- чистота поверхні: забезпечує чудову обробку поверхні, часто усуваючи потребу в додаткових процесах обробки.
- Матеріали: Шліфування підходить для твердих і абразивних матеріалів, включаючи загартовану сталь, кераміку та карбіди.
- Різноманітність методів подрібнення: Різні типи шліфувальних верстатів, наприклад плоскошліфувальні машини, циліндричні шліфувальні машини та безцентрові шліфувальні машини, задовольняють різні потреби обробки.
- Охолоджуюча рідина: Правильна охолоджуюча рідина має важливе значення під час шліфування, щоб запобігти перегріву та зберегти цілісність диска.
E. Електроерозійна обробка (EDM)
Електроерозійна обробка, або електроерозійна обробка, є нетрадиційним процесом точної обробки, який використовує електричні розряди для видалення матеріалу. Він особливо підходить для обробки складних і хитромудрих форм, а також твердих і термостійких матеріалів. Основні аспекти EDM включають:- Безконтактна обробка: EDM не передбачає прямого контакту між інструментом і деталлю, що знижує ризик зносу та пошкодження інструменту.
- Висока точність: EDM може досягти високої точності, що робить його придатним для застосувань, де важливі жорсткі допуски.
- Складні форми: Він відмінно підходить для обробки складних форм, штампів, прес-форм і компонентів з дрібними деталями.
- Електроерозія дроту та Електроерозія грузила: Є два основних типи електроерозійних верстатів: дротяна електроерозійна машина, у якій використовується дротяний електрод, і електроерозійна електророзійна машина з дротом, у якій використовується фасонний електрод.
- Повільний процес: EDM є відносно повільним у порівнянні з іншими методами обробки, що робить його найкращим для виконання невеликих обсягів високоточних завдань.
Допуски та контроль якості
Точна обробка вимагає прискіпливої уваги до деталей і суворого контролю якості, щоб забезпечити відповідність деталей встановленим стандартам. У цьому розділі ми розглянемо три найважливіші аспекти контролю якості в прецизійній обробці: визначення геометричних розмірів і допусків (GD&T), статистичний контроль процесу (SPC) і забезпечення якості.A. Геометричні розміри та допуски (GD&T)
Геометричні розміри та визначення допусків, часто скорочено GD&T, — це система, яка використовується для визначення та передачі дозволених варіацій розміру, форми, орієнтації та розташування елементів на деталі. GD&T життєво важливий у прецизійній обробці з таких причин:- Точне спілкуванняGD&T надає стандартизовану мову для інженерів, дизайнерів і машиністів, щоб точно передавати наміри проекту та вимоги до розмірів.
- Уточнення толерантності: Це допомагає визначити прийнятну варіацію в критичних розмірах, гарантуючи, що всі зацікавлені сторони розуміють допустимі відхилення.
- Покращена якість: GD&T сприяє підвищенню якості шляхом зменшення неоднозначності в специфікаціях конструкції, мінімізуючи ризик помилок під час обробки.
- Ефективність витрат: Чіткі специфікації GD&T можуть призвести до зниження витрат на виробництво, оскільки менша ймовірність того, що деталі будуть утилізовані або вимагатимуть переробки через непорозуміння чи неправильне тлумачення.
- Комплексна геометрія: це особливо корисно для деталей зі складною геометрією, гарантуючи, що всі елементи виготовляються відповідно до бажаних специфікацій.
B. Статистичний контроль процесу (SPC)
Статистичний контроль процесу (SPC) — це методологія контролю якості, яка використовує статистичні методи для моніторингу та контролю процесу обробки. SPC має важливе значення для точної обробки з таких причин:- Моніторинг процесу: SPC допомагає контролювати процеси обробки в режимі реального часу, виявляючи варіації або відхилення від бажаних параметрів.
- Раннє виявлення проблем: безперервно контролюючи процес, SPC дозволяє завчасно виявляти проблеми, які можуть призвести до деталей, що не відповідають специфікаціям, зменшуючи відходи та переробку.
- Прийняття рішень на основі даних: SPC покладається на дані та статистичний аналіз для прийняття обґрунтованих рішень щодо коригування процесу, гарантуючи, що процес обробки залишається в прийнятних межах.
- Покращена консистенція: SPC сприяє узгодженості процесу та зменшує ймовірність виробництва невідповідних деталей.
- Зменшення браку та переробки: Шляхом швидкого виявлення та вирішення змін процесу SPC мінімізує виробництво дефектних деталей, зменшуючи витрати на утилізацію та переробку.
C. Гарантія якості в прецизійній обробці
Гарантія якості в прецизійній обробці включає комплексний підхід до забезпечення того, щоб виготовлені деталі відповідали встановленим стандартам якості або перевищували їх. Він включає різні елементи, зокрема:- Процесна документація: Детальна документація процесів обробки, включаючи стандартні операційні процедури (SOP) і робочі інструкції, забезпечує послідовне виконання кожного кроку.
- Перевірка та вимірювання: Ретельна перевірка та вимірювання за допомогою точних приладів і методів метрології підтверджують, що деталі відповідають заданим допускам і стандартам якості.
- Калібрування: Регулярне калібрування обробного обладнання та вимірювальних приладів має важливе значення для підтримки точності та відстеження.
- Перевірка матеріалу: Перевірка властивостей, складу та якості матеріалу має вирішальне значення для забезпечення відповідності використовуваного матеріалу вимогам проекту.
- Навчання працівників: Програми навчання та підвищення кваліфікації для машиністів і персоналу з контролю якості гарантують, що вони володіють своїми ролями та обов’язками.
- Аналіз причин: Коли виявлено невідповідні частини, проводиться аналіз першопричини, щоб визначити джерело проблеми та вжити коригувальних дій.
- Постійне вдосконалення: Культура безперервного вдосконалення сприяє інноваціям і стимулює постійне вдосконалення процесів обробки та процедур контролю якості.
- Зворотній зв'язок з клієнтом: Збір і аналіз відгуків клієнтів допомагає визначити сфери, які потрібно вдосконалити, і узгоджує процеси обробки з очікуваннями клієнтів.
Висновок
A. Мистецтво і наука точної обробки
Прецизійна обробка знаходиться на перетині мистецтва та науки, де креативність, майстерність та інновації сходяться для виробництва високоточних деталей, які рухають промисловість і формують сучасний світ. Це і форма мистецтва, яка потребує майстерності та досвіду машиністів, які перетворюють сировину на витвори інженерної досконалості, і наука, яка спирається на передові технології, матеріалознавство та передові процеси для досягнення неперевершеної точності. Подорож точної обробки веде нас через розуміння матеріалів та їхніх властивостей, майстерне володіння ріжучими інструментами та механізмами, а також ретельний контроль процесів і допусків. Він охоплює мову геометричних розмірів і допусків, пильність статистичного контролю процесу та зобов'язання щодо забезпечення якості. Прецизійна обробка відіграє ключову роль у різноманітних галузях промисловості, від аерокосмічної та автомобільної до медичних приладів та електроніки, формуючи все від авіаційних двигунів до штучних суглобів і мікросхем. Це дозволяє створювати компоненти, які працюють із неперевершеною точністю та надійністю, часто розсуваючи межі можливого.B. Останні думки
Коли ми закінчуємо це дослідження прецизійної обробки, стає зрозуміло, що ця сфера стосується не лише створення деталей; мова йде про створення можливостей. Прагнення до точності стимулює інновації, розсуваючи межі того, чого можна досягти. Незалежно від того, чи йдеться про тонку майстерність, необхідну для створення складних механізмів годинника, чи про передову технологію, необхідну для виготовлення складних аерокосмічних компонентів, точна обробка є основою всього цього. Майбутнє точної обробки багатообіцяюче. Досягнення в матеріалознавстві, автоматизації та цифрових технологіях продовжують змінювати ландшафт. Мініатюризація, 3D-друк і практики екологічного виробництва стають дедалі помітнішими, відкриваючи нові горизонти для галузі. У світі, де точність важлива як ніколи, точна обробка залишається незамінною опорою сучасного машинобудування. Це свідчення людської винахідливості та нашого непохитного прагнення до досконалості в кожному аспекті виробництва. У міру зростання попиту на вищу точність і складніші компоненти точна обробка продовжуватиме розвиватися, вирішуючи виклики завтрашнього дня з тією самою відданістю та точністю, які визначали її протягом століть.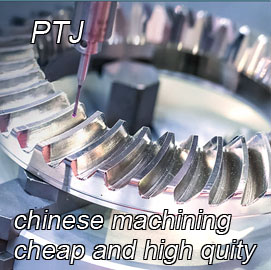
Наші Послуги
- 5 Обробка осей
- Фрезерування з ЧПУ
- Поворот cnc
- Механічна промисловість
- Процес обробки
- Обробка поверхонь
- Механічна обробка металу
- Обробка пластику
- Форма порошкової металургії
- Лиття під тиском
- Галерея запчастин
Приклади з практики
- Автозапчастини для металу
- Частини машин
- Світлодіодний радіатор
- Будівельні частини
- Мобільні частини
- Медичні частини
- Електронні частини
- Індивідуальна обробка
- частини велосипедів
Список матеріалів
- Обробка алюмінію
- Обробка титану
- Механічна обробка нержавіючої сталі
- Обробка міді
- Латунна обробка
- Суперсплавна обробка
- Загляньте в обробку
- Обробка УВМВ
- Однорідна механічна обробка
- Обробка PA6
- Обробка PPS
- Обробка тефлоном
- Механічна обробка інконеля
- Обробка інструментальної сталі
- Більше матеріалу
Галерея запчастин