Вичерпний посібник із налаштування токарного ріжучого інструменту
Налаштування ріжучого інструменту токарного верстата є фундаментальним навиком для будь-якого верстата, особливо коли він має справу з токарними верстатами з ЧПУ. Правильне налаштування інструменту має вирішальне значення для досягнення точних і точних результатів обробки. У цьому вичерпному посібнику ми заглибимося в складні деталі того, як налаштувати токарний ріжучий інструмент для токарної обробки з ЧПУ. Від основ компонентів токарного інструменту до передових методів оптимізації продуктивності різання, ця стаття має на меті забезпечити всебічне розуміння процесу. До кінця цього посібника ви матимете знання та навички, необхідні для впевненого й точного налаштування ріжучого інструменту на токарному верстаті, забезпечуючи оптимальні результати під час токарних операцій із ЧПУ.
Розуміння ріжучих інструментів токарного верстата
У світі обробки токарні ріжучі інструменти є незамінними компонентами для формування та перетворення вихідних матеріалів у деталі високої точності. Незалежно від того, чи працюєте ви з традиційними ручними токарними верстатами чи вдосконаленими токарними верстатами з ЧПК, глибоке розуміння ріжучих інструментів для токарних верстатів є важливим. У цьому розділі ми глибше розглянемо характеристики, функції та типи токарних різальних інструментів.
Характеристика ріжучих інструментів токарних верстатів
Різальні інструменти для токарних верстатів призначені для виконання різноманітних операцій обробки, таких як точіння, торцювання, нарізання канавок, нарізання різьби тощо. Ці інструменти мають кілька спільних характеристик:
- Твердість: Різальні інструменти для токарних верстатів зазвичай виготовляються зі швидкорізальної сталі (HSS), твердого сплаву або інших спеціалізованих інструментальних матеріалів. Ці матеріали вибираються через їхню твердість, що дозволяє інструменту витримувати високі температури та тиск, що виникають під час різання.
- Ріжучий край: Ріжуча кромка токарного інструменту - це частина, яка фактично видаляє матеріал із заготовки. Він розроблений, щоб бути гострим і точним, а геометрія ріжучої кромки може змінюватися залежно від конкретного завдання, для якого призначений інструмент.
- Хвостовик: Хвостовик токарного інструменту – це деталь, яка затискається в інструментотримачі. Це забезпечує стійкість і жорсткість інструменту під час роботи процес механічної обробки. Конструкції хвостовика можуть відрізнятися в залежності від типу інструменту та характеристик виробника.
- Тримач інструменту: Тримач інструменту є важливим компонентом, особливо в токарній обробці з ЧПК, оскільки він надійно утримує токарний інструмент на місці. Він повинен забезпечувати стабільність, точність і легкість регулювання для забезпечення оптимальної роботи інструменту.
- Геометрія: Геометрія ріжучого інструменту, включаючи передній кут, кут зазору та стружколом, відіграє значну роль у визначенні продуктивності інструменту. Правильна геометрія має важливе значення для досягнення ефективного видалення матеріалу та евакуації стружки.
- Покриття: Багато ріжучих інструментів для токарних верстатів постачаються зі спеціальними покриттями, такими як TiN (нітрид титану) або TiAlN (нітрид титану алюмінію), щоб збільшити термін служби інструменту, зменшити тертя та покращити продуктивність.
Функції токарних різальних інструментів
Різальні інструменти токарного верстата виконують кілька основних функцій у процесі обробки:
- Видалення матеріалу: Основною функцією ріжучих інструментів для токарного верстата є видалення матеріалу із заготовки. Це видалення може відбуватися шляхом повороту (обертання заготовки під час різання), торцювання (створення плоскої поверхні) або інших операцій.
- Контроль розмірів: Ріжучі інструменти відповідають за те, щоб розміри обробленої деталі відповідали бажаним характеристикам. Точний контроль необхідний для досягнення точних і стабільних результатів.
- Оздоблення поверхні: Якість обробки поверхні визначається гостротою ріжучого інструменту, його геометрією та використовуваними параметрами різання. Доглянутий і правильно налаштований ріжучий інструмент сприяє гладкій і тонкій обробці поверхні.
- Контроль мікросхем: Ефективний контроль стружки має важливе значення для запобігання накопиченню стружки та підтримки чистого та безпечного робочого середовища. Стружколом на деяких інструментах допомагає полегшити видалення стружки.
- Ефективність: Ріжучі інструменти для токарних верстатів розроблені, щоб зробити процеси обробки ефективними та економічно вигідними. Вони допомагають мінімізувати матеріальні відходи та оптимізувати термін служби інструменту, зменшуючи виробничі витрати.
Види токарних різальних інструментів
Ріжучі інструменти для токарних верстатів доступні в різних типах, кожен з яких призначений для конкретних завдань обробки. Ось кілька поширених типів:
- Токарні інструменти: Ці інструменти є універсальними і використовуються для циліндричних токарних операцій. Вони можуть формувати зовнішню і внутрішню поверхні заготовки.
- Бурові інструменти: Розточувальні інструменти використовуються для розширення або обробки наявних отворів. Вони створені для високої точності обробки отворів.
- Інструменти для розділення: Відрізні інструменти використовуються для відділення заготовки від більшої заготовки. Вони створюють чіткі лінії проділу з мінімальними відходами.
- Інструменти потоків: Різьбонарізні інструменти використовуються для нарізування різьби на заготовці. Вони бувають різних форм і розмірів для різних вимог до різьби.
- Інструменти для канавок: Інструменти для нарізання канавок створюють канавки або виїмки на заготовці, як правило, для розміщення ущільнювальних кілець, стопорних кілець або інших елементів.
- Облицювальні інструменти: Торцювальні інструменти призначені для створення плоских поверхонь на торці заготовки. Вони часто використовуються для отримання перпендикулярних поверхонь або видалення матеріалу з кінця заготовки.
Розуміння характеристик і функцій ріжучих інструментів для токарних верстатів має важливе значення для вибору правильного інструменту для конкретного завдання обробки. Вибір ріжучого інструменту може суттєво вплинути на якість та ефективність процесу обробки, що робить його критичним рішенням у будь-якій токарній операції. Крім того, належне технічне обслуговування та налаштування інструменту є життєво важливими для забезпечення стабільних і точних результатів, які будуть обговорюватися більш детально далі в цьому посібнику.
Види токарних різальних інструментів
Різальні інструменти для токарних верстатів бувають різних типів, кожен спеціально призначений для конкретного завдання обробки. Розуміння цих різних типів ріжучих інструментів і їх застосування має важливе значення для вибору правильного інструменту для певної роботи. Ось кілька поширених типів ріжучих інструментів для токарних верстатів:
Токарні інструменти:
- Інструмент із круглим носом: Використовується для токарних робіт загального призначення. Він має округлу ріжучу кромку і підходить як для чорнових, так і для фінішних різів.
- Алмазний інструмент: Завдяки своїй ромбовидній ріжучій кромці він ідеально підходить для точної обробки різних матеріалів, зокрема металів і пластмас.
- Інструмент з квадратним носом: Має квадратну ріжучу кромку і зазвичай використовується для точіння торців і плечей.
Бурові інструменти:Внутрішня розточувальна штанга: Використовується для збільшення та обробки наявних отворів у заготовці. Він створений для точності та може створювати точні внутрішні розміри.
Інструменти для розділення:Роздільне лезо: Ці інструменти використовуються для відрізання заготовки з більшого заготовки. Вони створюють чітку лінію проділу з мінімальними відходами.
Інструменти потоків:
- Інструмент для нарізання різьби: Призначений для створення зовнішньої різьби на заготовці. Вони бувають різних форм і розмірів для різних вимог до різьби.
- Інструмент для різьблення: Використовується для переслідування або відновлення існуючих потоків. Ці інструменти зазвичай використовуються для ремонту різьби.
Інструменти для канавок:Інструмент для канавок: Ці інструменти створюють канавки або виїмки на заготовці, часто для розміщення ущільнювальних кілець, стопорних кілець або інших елементів.
Облицювальні інструменти:Інструмент для облицювання: Використовується для створення плоских поверхонь на торці заготовки. Його часто використовують для отримання перпендикулярних поверхонь або видалення матеріалу з торця заготовки.
Інструменти для відрізання та обробки канавок:Комбінований інструмент: Ці універсальні інструменти призначені як для відрізання, так і для обробки канавок, заощаджуючи час і змінюючи інструмент.
Інструменти для нарізання різьби та канавок:Комбінований інструмент для нарізання різьби та канавок: Ідеально підходить для робіт, які вимагають нарізання різьби та канавок на одній заготовці.
Інструменти для зняття фасок:Інструмент для зняття фасок: Використовується для створення фасок або скошених країв на заготовці. Для поліпшення зовнішнього вигляду та полегшення складання оброблених деталей часто застосовуються фаски.
Інструменти для накатки:Інструмент для накатки: Накатка – це процес створення текстурованого візерунка на заготовці, як правило, для покращення зчеплення або естетики. Інструменти для накатки бувають різних моделей і дизайнів.
Інструменти для формування:Інструмент форми: Ці інструменти спеціально розроблені для певної геометрії деталей, часто використовуються для виготовлення складних і нестандартних форм.
Спеціальні інструменти:Інструменти профілю: Використовується для створення складних профілів на заготовці.
Торцювальний і токарний інструмент: Вони призначені як для облицювання, так і для токарних операцій.
Інструменти для обрізання: Призначений для розрізання заготовки для створення окремих частин або видалення зайвого матеріалу.
Вибір правильного ріжучого інструменту залежить від таких факторів, як матеріал, що обробляється, бажана обробка, необхідні розміри та конкретна операція, що виконується. Важливо вибрати відповідний інструмент і правильно його обслуговувати, щоб забезпечити ефективну та точну обробку. Правильний вибір інструменту разом із правильним налаштуванням і регулюванням має вирішальне значення для досягнення високоякісних результатів токарних операцій.
Складові частини токарного різального інструменту
Токарний ріжучий інструмент — це прецизійний інструмент, призначений для формування, різання та видалення матеріалу з заготовки. Щоб зрозуміти, як він працює та як його правильно налаштувати, дуже важливо ознайомитися з його різними компонентами. Ось основні компоненти токарного різального інструменту:
- Тримач інструменту:Тримач інструменту - це частина, яка фіксує ріжучий інструмент на місці. Він кріпиться до інструментальної стійки токарного верстата та забезпечує необхідну жорсткість і стабільність для операцій обробки. Тримачі для інструментів мають різні конструкції для розміщення різних типів ріжучих інструментів.
- Хвостовик:Хвостовик - це частина ріжучого інструменту, яка вставляється в інструментотримач. Зазвичай він циліндричний і надійно закріплений у тримачі. Розміри та форма хвостовика можуть відрізнятися залежно від типу та конструкції інструменту.
- Ріжучий край:Ріжуча кромка - це гостра частина інструменту, яка контактує з матеріалом і видаляє його з заготовки. Якість ріжучої кромки та її геометрія значно впливають на ефективність різання та обробку поверхні. Дуже важливо підтримувати гостроту та точність ріжучої кромки.
- Вставити:Багато сучасних ріжучих інструментів використовують змінні пластини, які зазвичай виготовляються з твердих матеріалів, таких як твердий сплав або кераміка. Ці пластини мають ріжучу геометрію та закріплені в кишені на різальному інструменті. Їх можна повернути або замінити, якщо вони зношені або пошкоджені, подовжуючи термін служби інструменту.
- Ніс інструменту:Носик інструменту – це самий кінчик ріжучого інструменту, де з’єднуються ріжуча кромка та пластина (якщо використовується). Носик інструмента повинен бути точно розташований і вирівняний для точної обробки. Деякі токарні ріжучі інструменти мають регульований радіус носа інструмента для кращого контролю над продуктивністю інструменту.
- Фланг інструменту:Бічна сторона інструменту - це бічна поверхня ріжучого інструменту, яка не є частиною ріжучої кромки. Належні кути зазору на боці інструменту забезпечують відведення стружки та зменшують тертя між інструментом і заготовкою.
- Передня поверхня інструменту:Передня поверхня ріжучого інструменту звернена до заготовки. Кут і стан передньої поверхні впливають на формування стружки та ефективність процесу різання. Передній кут є критично важливим аспектом геометрії інструменту.
- Кут рельєфу інструменту:Кут рельєфу - це кут між боковою стороною інструменту та віссю інструменту. Це гарантує, що ріжуча кромка не стирається об заготовку, зменшуючи тертя та виділення тепла.
- Кут зазору інструменту:Кут зазору - це кут між передньою поверхнею і поверхнею заготовки. Це забезпечує плавне переміщення стружки та запобігає перетину між інструментом і заготовкою.
- Стружколом (за наявності):Деякі ріжучі інструменти, особливо ті, що використовуються для чорнових операцій, мають стружколом, канавку або виїмку на передній поверхні. Стружколом допомагає контролювати утворення стружки та покращує відведення стружки.
Правильна збірка, вирівнювання та технічне обслуговування цих компонентів є важливими для досягнення точної та ефективної обробки. Вибір ріжучого інструменту та його налаштування повинні бути пристосовані до конкретної операції обробки та матеріалу, що обробляється. Регулярний огляд і технічне обслуговування компонентів ріжучого інструменту також необхідні для забезпечення постійних і високоякісних результатів.
Вибір правильного різального інструменту для роботи
Вибір правильного ріжучого інструменту є критичним рішенням у будь-якій операції обробки, оскільки він значною мірою впливає на якість, ефективність і точність роботи. Вибираючи відповідний різальний інструмент для конкретної роботи, слід враховувати кілька факторів. Ось інструкція щодо вибору правильного ріжучого інструменту для вашого проекту обробки:
1. Матеріал заготовки:
Матеріал, який ви обробляєте, є одним із найважливіших факторів у виборі інструменту. Різні матеріали мають різну твердість, теплопровідність і абразивність. Зверніть увагу на наступне:
- Твердість: Тверді матеріали, такі як загартована сталь або кераміка, потребують ріжучих інструментів із твердими ріжучими кромками, таких як твердосплавні пластини, щоб витримувати високі сили різання.
- М'які матеріали: Для м’яких матеріалів, таких як алюміній або пластик, може бути достатньо швидкорізальної сталі (HSS) або інших інструментальних матеріалів.
2. Механічна обробка:
Конкретна операція, яку ви виконуєте, наприклад токарна обробка, фрезерування, свердління, нарізка різьблення або канавок, визначатиме тип ріжучого інструменту, який вам потрібен. Різні інструменти призначені для різних завдань, і вибір правильного гарантує оптимальну продуктивність.
3. Швидкість різання та швидкість подачі:
Визначте необхідну швидкість різання та швидкість подачі на основі матеріалу та операції обробки. Виробники ріжучого інструменту надають рекомендації щодо цих параметрів на основі конструкції інструменту та матеріалу, що обробляється. Дотримання цих рекомендацій має вирішальне значення для досягнення бажаних результатів.
4. Геометрія інструменту:
Враховуйте геометрію ріжучого інструменту, включаючи передній кут, кут зазору та радіус носа інструмента. Геометрія інструменту повинна відповідати матеріалу і виду різу. Наприклад, позитивний передній кут підходить для м’яких матеріалів, а негативний – для твердіших.
5. Розміри заготовки:
Розмір і розміри заготовки також впливають на вибір інструменту. Деякі ріжучі інструменти краще підходять для чорнових операцій для швидкого видалення сипучого матеріалу, тоді як інші призначені для фінішної обробки для досягнення точних розмірів і обробки поверхні.
6. Вимоги до обробки поверхні:
Якщо вам потрібна конкретна обробка поверхні, виберіть ріжучий інструмент з відповідною геометрією та гостротою. Інструменти для фінішної обробки призначені для отримання більш гладкої поверхні, тоді як інструменти для чорнової обробки більш ефективні для видалення матеріалу.
7. Матеріал інструменту:
Вибір матеріалу інструменту має вирішальне значення. Інструменти з твердого сплаву, швидкорізальної сталі (HSS), кераміки та інструменти з покриттям мають свої переваги та обмеження. У своєму рішенні враховуйте такі фактори, як термін служби інструменту, зносостійкість і вартість матеріалу інструменту.
8. Охолоджуюча рідина та мастило:
Подумайте, чи потрібна операція різання охолоджувачем чи мастилом. Деякі матеріали виділяють надмірне тепло під час обробки, і використання відповідної охолоджувальної рідини або мастила може подовжити термін служби інструменту та покращити ефективність різання.
9. Покриття для інструментів:
Багато сучасних ріжучих інструментів мають спеціальні покриття, такі як TiN (нітрид титану) або TiAlN (нітрид титану алюмінію), щоб покращити зносостійкість і зменшити тертя. Виберіть інструмент із відповідним покриттям для конкретного застосування.
10. Витрати:
Співвідношення вартості ріжучого інструменту з його продуктивністю та довговічністю має вирішальне значення. Хоча інструменти преміум-класу можуть запропонувати довший термін експлуатації та кращу продуктивність, важливо знайти баланс, який відповідає бюджету вашого проекту.
11. Сумісність тримача інструменту та машини:
Переконайтеся, що вибраний ріжучий інструмент сумісний із системою тримача інструменту вашого токарного верстата чи обробного центру. Тримач інструменту повинен забезпечувати стійкість і жорсткість ріжучого інструменту в процесі обробки.
Зрештою, правильний ріжучий інструмент для роботи залежатиме від комбінації цих факторів. Завжди звертайтеся до рекомендацій виробника інструменту та зверніться за порадою до досвідчених машиністів або експертів з інструментів, якщо ви не впевнені. Правильний вибір і налаштування інструменту є основою для досягнення ефективних і точних результатів обробки.
Налаштування ріжучого інструменту токарного верстата
Налаштування токарного різального інструменту для токарної обробки з ЧПУ є систематичним процесом, який включає кілька важливих етапів. Кожен крок є життєво важливим для забезпечення правильного розташування та вирівнювання ріжучого інструменту, що зрештою призводить до точної та ефективної обробки. Розглянемо процес крок за кроком:
Крок 1: Підготовка токарного верстата та заготовки
Перш ніж налаштувати ріжучий інструмент, важливо підготувати токарний верстат і заготовку:
- Закріпіть заготовку: Переконайтеся, що деталь надійно закріплена в токарному патроні або цанговому патроні. Переконайтеся, що він обертається плавно, без будь-яких хитань і вібрацій.
- Безпека: Переконайтеся, що всі заходи безпеки вжиті, включаючи використання відповідних засобів індивідуального захисту (ЗІЗ) і правильне налаштування токарного верстата.
Крок 2: Вибір правильного тримача інструменту
Тримач інструменту є критично важливим компонентом у процесі налаштування. Виберіть відповідний тримач інструменту на основі таких факторів, як тип ріжучого інструменту, операція, що виконується, і система опори інструменту токарного верстата.
- Підберіть тримач інструменту до ріжучого інструменту: Переконайтеся, що тримач інструменту сумісний із типом і розміром ріжучого інструменту, який ви збираєтеся використовувати.
- Жорсткість тримача інструменту: Виберіть тримач інструменту, який забезпечує стабільність і жорсткість. Це особливо важливо у високоточних програмах.
Крок 3: Встановлення ріжучого інструменту
Встановлення ріжучого інструменту передбачає його надійне та правильне закріплення у тримачі:
- Закріпіть ріжучий інструмент: Вставте ріжучий інструмент у тримач інструменту та затягніть будь-які затискні механізми, наприклад установчі гвинти або цанги. Переконайтеся, що інструмент надійно тримається.
- Орієнтація: Переконайтеся, що ріжучий інструмент правильно орієнтований відносно заготовки. Інструмент слід розташувати таким чином, щоб зачепити деталь під потрібним кутом і глибиною.
Крок 4: Налаштування висоти інструменту та вирівнювання центральної лінії
Правильна висота інструменту та вирівнювання центральної лінії мають вирішальне значення для досягнення точних розмірів обробки:
- Регулювання висоти інструменту: Відрегулюйте висоту інструмента, щоб вирівняти його з центральною лінією шпинделя токарного верстата. Щоб установити інструмент на правильну висоту, скористайтеся висотоміром або тестовою планкою.
- Вирівнювання по центральній лінії: Переконайтеся, що інструмент вирівняно з центральною лінією шпинделя токарного верстата. Несумісність може призвести до нецентральної обробки, що вплине на точність деталі.
Крок 5: Налаштування компенсації радіуса носа інструмента
Для токарної обробки з ЧПК компенсація радіуса вершини інструменту враховує геометрію ріжучого інструменту. Це особливо важливо при використанні інструментів вставки:
- Визначте радіус носа інструмента: Виміряйте або знайдіть точний радіус носа пластини ріжучого інструменту, яку ви використовуєте.
- Введіть значення радіуса: У керуючому програмному забезпеченні ЧПК введіть виміряне значення радіуса вершини інструмента, щоб гарантувати, що верстат компенсує геометрію інструменту під час обробки.
Крок 6: Встановлення корекції інструменту
Корекції інструменту враховують варіації в розмірах інструменту та геометрії заготовки. Вони забезпечують точне налаштування положення інструменту для обробки:
- Виберіть правильне зсув інструмента: Визначте відповідне значення корекції інструмента на основі геометрії інструмента та операції обробки. Це значення зміщення компенсує будь-які розбіжності.
- Введіть значення зміщення: Введіть вибрані значення зсуву в програмне забезпечення керування ЧПК. Ці значення вкажуть машині, як точно відрегулювати положення інструменту.
Протягом усього процесу налаштування інструменту використовуйте прецизійні вимірювальні прилади, такі як мікрометри, ростоміри та циферблатні індикатори, щоб перевірити та точно налаштувати центрування інструменту. Регулярно перевіряйте та доглядайте за ріжучим інструментом, щоб переконатися, що він залишається гострим і в хорошому стані, оскільки добре обслуговуваний інструмент сприяє стабільним і точним результатам обробки.
Правильне налаштування ріжучого інструменту токарного верстата на цих етапах має вирішальне значення для досягнення оптимальних результатів токарних операцій з ЧПУ. Точність і увага до деталей під час налаштування інструменту є ключовими факторами у виробництві високоякісних оброблених деталей.
Оптимізація параметрів різання для токарної обробки з ЧПУ
Оптимізація параметрів різання має важливе значення для досягнення ефективних і якісних токарних операцій з ЧПУ. Чотири ключові аспекти, які слід враховувати під час оптимізації параметрів різання, це швидкість і подача, глибина різання, ріжучі рідини та мастила, а також керування терміном служби інструменту.
1. Швидкості та канали:
- a. Швидкість різання (швидкість поверхні):Швидкість різання, яку часто називають швидкістю поверхні, - це швидкість, з якою заготовка та ріжучий інструмент взаємодіють. Вона вимірюється в поверхневих футах за хвилину (SFM) або метрах за хвилину (м/хв). Щоб оптимізувати швидкість різання, враховуйте матеріал, що обробляється, і матеріал інструмента. Наприклад, інструменти зі швидкорізальної сталі (HSS) мають нижчу рекомендовану швидкість різання, ніж твердосплавні інструменти. Зверніться до даних виробника інструменту або довідників з обробки, щоб визначити рекомендовані швидкості різання для конкретних матеріалів і інструментів.
- b. Швидкість подачі:Швидкість подачі - це лінійна швидкість, з якою ріжучий інструмент просувається в заготовку. Він вимірюється в дюймах на оберт (IPR) або міліметрах на оберт (мм/об). Щоб оптимізувати швидкість подачі, враховуйте такі фактори, як властивості матеріалу, геометрія інструменту та бажана обробка поверхні. Вищі швидкості подачі, як правило, більш продуктивні, але можуть вимагати міцніших інструментів.
- в. Співвідношення швидкості різання та швидкості подачі:Збалансування швидкості різання та швидкості подачі має вирішальне значення для ефективного видалення матеріалу. Збільшення швидкості різання, як правило, дозволяє збільшити швидкість подачі, але обидва вони повинні регулюватися разом, щоб запобігти зносу інструменту та перегріву.
2. Глибина різання:
- a. Глибина різання (DOC):Глибина різання - це відстань, на яку ріжучий інструмент проникає в заготовку. Важливо враховувати матеріал і можливості інструменту. Оптимізуйте глибину різання на основі твердості матеріалу, міцності та жорсткості інструменту. Неглибокі розрізи можуть знадобитися для більш твердих матеріалів, тоді як більш глибокі розрізи можна досягти для більш м’яких матеріалів.
- b. Осьова та радіальна глибина різання:Під час точіння з ЧПУ враховуйте як осьову (вздовж довжини заготовки), так і радіальну (по діаметру заготовки) глибину різання. Оптимальна глибина для кожного буде відрізнятися в залежності від операції та матеріалу.
3. Ріжучі рідини та мастила:
- a. Вибір правильної ріжучої рідини:Рідини для різання мають важливе значення для розсіювання тепла, зменшення тертя та покращення відводу стружки. Виберіть відповідну рідину для різання на основі матеріалу та операції обробки. Водорозчинна охолоджуюча рідина, мінеральна олива або синтетична охолоджуюча рідина можуть бути кращими для різних матеріалів.
- b. Правильне застосування:Ефективно нанесіть ріжучу рідину на зону різання, щоб забезпечити належне змащення та охолодження. Залежно від можливостей машини це можна зробити за допомогою систем охолодження, системи туману або подачі охолоджуючої рідини через інструмент.
- в. Моніторинг і технічне обслуговування:Регулярно контролюйте рівень, стан і забруднення СОЖ, щоб забезпечити їх ефективність. Обслуговуйте системи ріжучої рідини, щоб запобігти таким проблемам, як ріст і розпад бактерій.
4. Керування ресурсом інструменту:
- a. Перевірка та технічне обслуговування інструменту:Впроваджуйте планову програму перевірки та обслуговування інструментів, щоб переконатися, що інструменти знаходяться в хорошому стані. Тупі або пошкоджені інструменти можуть призвести до низької якості обробки та скорочення терміну служби інструменту.
- b. Графік заміни інструменту:Створіть графік заміни інструменту на основі таких факторів, як знос інструменту, час безвідмовної роботи машини та вимоги до виробництва. Це допомагає запобігти неочікуваним поломкам інструменту та підтримувати постійну якість обробки.
- в. Оптимізація ресурсу інструменту:Деякі інструментальні матеріали та покриття забезпечують довший термін служби. Розгляньте можливість використання високопродуктивного інструменту, щоб оптимізувати термін служби інструменту та скоротити час простою виробництва.
- d. Контроль стружки інструменту:Ефективний контроль за стружколомом, включаючи використання стружколомів і правильну геометрію інструменту, може подовжити термін служби інструменту за рахунок зменшення зносу, викликаного стружкою.
Оптимізація параметрів різання при токарній обробці з ЧПУ є безперервним процесом. Щоб знайти найкращі параметри для конкретного застосування, можуть знадобитися експерименти та точне налаштування. Регулярно контролюйте та регулюйте ці параметри, щоб забезпечити оптимальну продуктивність обробки, термін служби інструменту та якість деталей. Правильно оптимізовані параметри різання не тільки підвищують ефективність обробки, але й знижують знос інструменту та, зрештою, витрати на виробництво.
Усунення поширених проблем у налаштуваннях інструментів
Усунення типових несправностей під час налаштування інструменту є важливою навичкою для верстатників і операторів ЧПК. Розуміння та вирішення цих проблем може допомогти підтримувати точність і якість операцій обробки. Ось деякі поширені проблеми з налаштуванням інструменту та їх вирішення:
1. Балаканина інструментів:
Проблема: Скреготіння інструменту виникає, коли ріжучий інструмент вібрує під час процесу обробки, що призводить до поганої обробки поверхні, зносу інструменту та можливого пошкодження заготовки.
Рішення:
- Зменшити швидкість або збільшити подачу: Відрегулюйте параметри різання, зменшивши швидкість різання або збільшивши швидкість подачі. Ця зміна може зменшити вібрацію та зменшити тріскотіння.
- Перевірка жорсткості інструменту: Переконайтеся, що тримач інструменту та інструмент правильно закріплені та що інструмент не висувається надто далеко від тримача.
- Перевірте затиск заготовки: Переконайтеся, що деталь надійно закріплена, щоб запобігти вібрації, пов’язаній з деталлю.
- Використовуйте методи зволоження: Деякі машини оснащені функціями гасіння вібрацій. Якщо є, подумайте про їх використання.
- Виберіть більш жорсткий інструмент: Жорсткіший інструмент, наприклад із меншою кількістю канавок, може допомогти зменшити тріскотіння.
2. Погана обробка поверхні:
Проблема: Погана обробка поверхні може бути результатом проблем із налаштуванням інструменту або параметрами різання, що призводить до шорсткості або нерівності поверхонь заготовки.
Рішення:
- Перевірте геометрію інструменту: Переконайтеся, що геометрія ріжучого інструменту підходить для операції. Гострий інструмент із правильною геометрією має вирішальне значення для досягнення якісної обробки поверхні.
- Оптимізація параметрів різання: Відрегулюйте швидкість різання, швидкість подачі та глибину різання, щоб знайти найкраще поєднання для конкретного матеріалу та операції.
- Перевірте знос інструменту: Огляньте інструмент на наявність слідів зносу або пошкоджень, наприклад, сколів на краях. За потреби замініть або відшліфуйте інструмент.
- Використовуйте відповідну ріжучу рідину: Правильне змащування та охолодження може значно вплинути на якість поверхні. Використовуйте правильну ріжучу рідину для матеріалу та роботи.
- Мінімізація вібрації: Усуньте проблеми з вібрацією, щоб уникнути нерівностей на поверхні.
3. Неточності розмірів:
Проблема: Деталі можуть мати неправильні розміри через неправильне розташування інструментів або знос інструментів.
Рішення:
- Перевірте налаштування інструменту: Переконайтеся, що інструмент правильно налаштовано на правильну висоту та вирівняно відносно заготовки.
- Калібрування машини: Переконайтеся, що верстат з ЧПК правильно відкалібрований і що він точно інтерпретує корекції інструменту та дані інструменту.
- Відрегулюйте зміщення інструменту: Виправте будь-які помилки в корекції інструменту, точно вимірявши інструмент і ввівши належні значення корекції в ЧПК.
- Перевірте знос інструменту: Регулярно перевіряйте ріжучий інструмент на знос і замінюйте або переточуйте його, якщо це необхідно.
4. Проблеми з контролем мікросхем:
Проблема: Неналежний контроль стружки може призвести до таких проблем, як забивання стружки, погане відведення стружки та пошкодження заготовки чи інструменту.
Рішення:
- Виберіть правильну геометрію інструменту: Виберіть ріжучий інструмент із відповідним стружколомом або геометрією відповідно до матеріалу та роботи.
- Оптимізація параметрів різання: Регулюйте швидкість подачі, швидкість різання та глибину різання, щоб оптимізувати утворення стружки та її видалення.
- Використовуйте достатню мастило: Правильне використання рідин для різання може допомогти змастити та полегшити відведення стружки.
- Перевірте вирівнювання інструмента та заготовки: Переконайтеся, що інструмент правильно вирівняно з деталлю, щоб запобігти проблемам, пов’язаним зі стружкою.
5. Поломка інструменту:
Проблема: Поломка інструменту може статися через надмірне зусилля, неправильне налаштування інструменту або проблеми, пов’язані з матеріалом.
Рішення:
- Оптимізація параметрів різання: Зменште сили різання, регулюючи такі параметри, як швидкість подачі, швидкість різання та глибина різання.
- Перевірте налаштування інструменту: Переконайтеся, що інструмент надійно закріплений у тримачі інструменту та правильно вирівняний.
- Використовуйте належний матеріал інструменту: Виберіть правильний інструментальний матеріал для конкретного матеріалу, який ви обробляєте. Наприклад, твердосплавні інструменти краще підходять для твердих матеріалів.
- Перевірте знос інструменту: Регулярно перевіряйте інструмент на ознаки зносу та замінюйте його, перш ніж він стане надмірно зношеним і схильним до поломки.
Вирішення цих поширених проблем із налаштуванням інструменту вимагає поєднання належного навчання, регулярного технічного обслуговування та систематичного підходу до усунення несправностей. Здатність діагностувати та вирішувати проблеми, пов’язані з інструментом, має вирішальне значення для досягнення високоякісних та ефективних результатів обробки.
У Висновку
Процес налаштування та оптимізації різальних інструментів токарного верстата для токарної обробки з ЧПК є ключовим аспектом обробки, який значно впливає на якість, ефективність і точність виробничих процесів. Глибоке розуміння компонентів і функцій ріжучих інструментів, а також факторів, пов’язаних з вибором інструментів, має важливе значення для машиністів і операторів ЧПК.
Правильне налаштування ріжучого інструменту передбачає систематичний підхід, починаючи від підготовки токарного верстата та заготовки до вибору правильного тримача інструменту, встановлення інструменту, регулювання висоти інструменту та вирівнювання центральної лінії, а також налаштування компенсації радіуса вершини інструменту та зміщення інструменту. Кожен крок відіграє ключову роль у досягненні точних і ефективних результатів обробки.
Оптимізація параметрів різання, включаючи швидкість і подачу, глибину різання, ріжучі рідини та керування ресурсом інструменту, є ще одним важливим аспектом токарної обробки з ЧПУ. Ретельно підбираючи правильні параметри, машинисти можуть підвищити продуктивність, зберегти довговічність інструменту та покращити якість обробки поверхні.
Нарешті, здатність вирішувати поширені проблеми з налаштуванням інструменту, такі як стукіт інструменту, погана обробка поверхні, неточності розмірів, проблеми з контролем стружки та поломка інструменту, має важливе значення для підтримки постійних і високоякісних результатів обробки. Виявлення цих проблем і впровадження відповідних рішень гарантує безперебійність та ефективність процесу обробки.
Загалом, повне розуміння ріжучих інструментів токарного верстата та їх налаштування в поєднанні з можливістю оптимізації параметрів різання та усунення несправностей дає змогу машиністам досягати найкращих результатів у токарних операціях з ЧПУ. Постійне навчання, навчання та досвід є ключовими для вдосконалення цих навичок і забезпечення успішних процесів обробки.
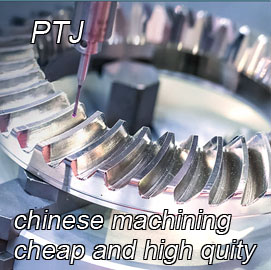
- 5 Обробка осей
- Фрезерування з ЧПУ
- Поворот cnc
- Механічна промисловість
- Процес обробки
- Обробка поверхонь
- Механічна обробка металу
- Обробка пластику
- Форма порошкової металургії
- Лиття під тиском
- Галерея запчастин
- Автозапчастини для металу
- Частини машин
- Світлодіодний радіатор
- Будівельні частини
- Мобільні частини
- Медичні частини
- Електронні частини
- Індивідуальна обробка
- частини велосипедів
- Обробка алюмінію
- Обробка титану
- Механічна обробка нержавіючої сталі
- Обробка міді
- Латунна обробка
- Суперсплавна обробка
- Загляньте в обробку
- Обробка УВМВ
- Однорідна механічна обробка
- Обробка PA6
- Обробка PPS
- Обробка тефлоном
- Механічна обробка інконеля
- Обробка інструментальної сталі
- Більше матеріалу