Технологія обробки поверхні алюмінієвого сплаву
Технологія обробки поверхні алюмінієвого сплаву
Алюміній має багато переваг, таких як низька щільність, висока питома міцність, хороша корозійна стійкість, висока електро- і теплопровідність, зварюваність, хороша пластичність, легка обробка та формування, а також чудові властивості декорування поверхні. Алюмінієвий сплав виготовляється з чистого алюмінію шляхом додавання деяких легуючих елементів. Алюмінієвий сплав краще, ніж чистий алюміній. Алюміній має кращі фізико-механічні властивості. Через відносно активну природу алюмінію він може спонтанно утворювати плівку аморфного оксиду в повітрі, завдяки чому він має кращу корозійну стійкість в атмосфері, але товщина плівки становить лише близько 4 нм, а структура є пухкою, тонкою і тонкою. Пориста, низька твердість, погана зносостійкість і низька механічна міцність, тому для досягнення мети захисту необхідно вручну покрити алюмінієву поверхню плівкою. Зазвичай цього можна досягти шляхом окислювальної обробки, гальванічного покриття та зовнішнього покриття. |
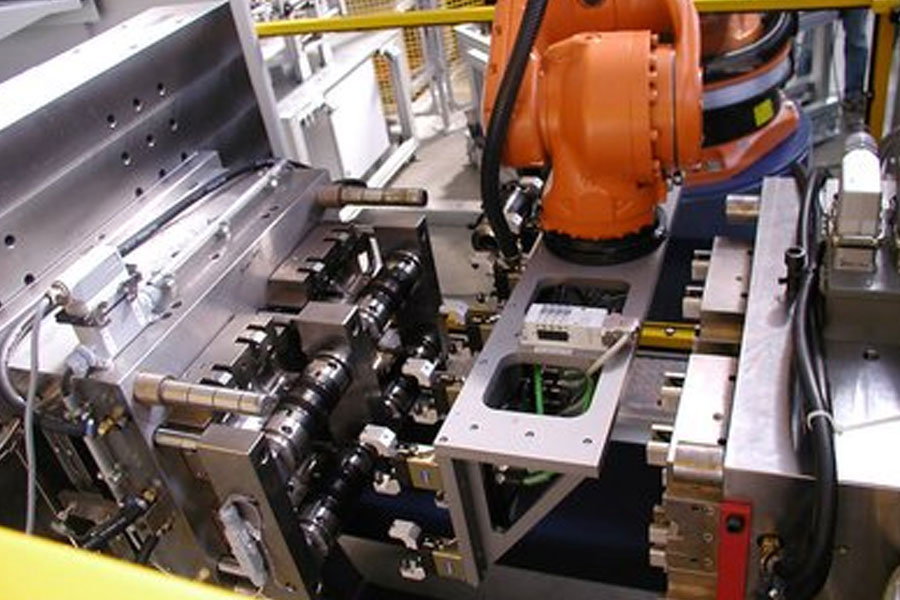
1 Окислювальна обробка
Окислювальна обробка в основному полягає в анодному окисленні, хімічному окисленні та мікродуговому окисленні. Xu Lingyun та ін. [1] досліджували механічні властивості та корозійну стійкість алюмінієвого сплаву А356, виконуючи три різні обробка поверхоньs: хімічне окислення, анодування та мікродугове окислення. Завдяки технології SEM, випробуванню на знос і корозійній стійкості, морфологія поверхні, товщина оксидного шару, зносостійкість і корозійна стійкість алюмінієвого сплаву через три обробка поверхоньs були проаналізовані та детально порівняні. Результати показують, що після різн обробка поверхоньs, поверхня алюмінієвого сплаву може утворювати оксидні плівки різної товщини, твердість поверхні та зносостійкість значно покращуються, а також у різному ступені покращується корозійна стійкість сплаву. З точки зору загальної продуктивності, мікродугове окислення краще, ніж анодне окислення, а анодне окислення краще, ніж хімічне.
1.1 Анодування
Анодування також називають електролітичним окисленням, яке по суті є обробкою електрохімічним окисленням. Він використовує алюміній та алюмінієві сплави як аноди в електролітиці, а оксидна плівка (в основному шар Al 2 O 3 ) утворюється на поверхні алюмінію після включення живлення. Оксидна плівка, отримана анодним окисленням, має хорошу корозійну стійкість, стабільний процес і легке просування. Це найпростіший і найпоширеніший метод обробки поверхні алюмінію та алюмінієвих сплавів у сучасній моїй країні. Анодна оксидна плівка має багато характеристик: бар’єрний шар оксидної плівки має високу твердість, хорошу зносостійкість, хорошу корозійну стійкість, хороший ізоляційний матеріал, високу хімічну стабільність і може використовуватися як базова плівка для покриття; оксидна плівка має багато отворів і може бути використана. Використовується в різних фарбах і фарбах для підвищення декоративності алюмінієвої поверхні; теплопровідність оксидної плівки дуже низька, і це хороша теплоізоляція і термостійкий захисний шар. Однак, нинішнє анодне окислення алюмінію та алюмінієвих сплавів зазвичай використовує хромат як окисник, що спричиняє велике забруднення навколишнього середовища.
У поточних дослідженнях анодування алюмінію та алюмінієвих сплавів увага також приділяється використанню характеристик певних іонів металів для оптимізації властивостей алюмінію та алюмінієвих сплавів. Наприклад, Tian Lianpeng [2] використав технологію іонної імплантації для введення титану на поверхню алюмінієвого сплаву, а потім додатково здійснив анодування для отримання алюмінієво-титанового композитного анодованого плівкового шару, який зробив поверхню анодованої плівки більш плоскою та однорідною. , а також покращено анодування алюмінієвого сплаву. Щільність плівки; Імплантація іонів титану може значно підвищити корозійну стійкість плівки анодного оксиду алюмінієвого сплаву в кислотних і лужних розчинах NaCl, але це не впливає на аморфну структуру плівки анодного оксиду алюмінієвого сплаву. Імплантація іонів нікелю робить структуру поверхні та морфологію плівки анодного оксиду алюмінію більш щільною та однорідною. Інжектований нікель існує у формі металевого нікелю та оксиду нікелю в анодній оксидній плівці з алюмінієвого сплаву.
1.2 Хімічне окислення
Хімічне окислення відноситься до методу нанесення покриття, при якому чиста алюмінієва поверхня взаємодіє з киснем в окисному розчині за допомогою хімічної дії при певних температурних умовах з утворенням щільної оксидної плівки. Існує багато методів хімічного окислення алюмінію та алюмінієвих сплавів, залежно від природи розчину.
Його можна розділити на лужний і кислий. За характером плівки її можна розділити на оксидну плівку, фосфатну плівку, хроматну плівку та плівку хромової кислоти-фосфату. Оксидна плівка, отримана шляхом хімічного окислення деталей з алюмінію та алюмінієвих сплавів, має товщину приблизно 0.5~4 мкм. Вона має низьку зносостійкість і меншу корозійну стійкість, ніж анодна оксидна плівка. Він не підходить для використання окремо, але він має певну стійкість до корозії та хороші фізичні властивості. Вбираюча здатність є хорошою грунтовкою для фарбування. Фарба після хімічного окислення алюмінію та алюмінієвого сплаву може значно покращити силу зчеплення між підкладкою та покриттям, а також підвищити корозійну стійкість алюмінію [3].
1.3 Метод мікродугового окислення
Технологія мікродугового окислення також відома як технологія мікроплазмового окислення або технологія анодного іскрового осадження, яка є свого роду зростанням на місці за допомогою розряду мікроплазми на поверхні металу та його сплавів. Окислення
Нова технологія керамічної мембрани. Поверхнева плівка, утворена цією технологією, має сильну силу зчеплення з підкладкою, високу твердість, зносостійкість, корозійну стійкість, високу стійкість до теплового удару, хорошу електричну ізоляцію плівки та високу напругу пробою. Мало того, технологія використовує передовий метод нагріву мікроплазмової дуги з надзвичайно високою щільністю енергії, структура матриці не зачіпається, а процес не є складним і не викликає забруднення навколишнього середовища. Це нова перспективна технологія обробки поверхні матеріалів. Він стає гарячою точкою досліджень у сфері міжнародних технологій обробки поверхні матеріалів. Чжан Джуго та ін.
Використаний механічна обробка алюмінію сплав LY12 в якості досліджуваного матеріалу, використовували обладнання для мікродугового окислення MAO240/750, товщиноміри TT260 і скануючий електронний мікроскоп AMARY-1000B для дослідження впливу напруги дуги, густини струму та часу окислення на шар кераміки. Вплив на продуктивність. Завдяки серії експериментів з процесом мікродугового окислення алюмінієвого сплаву з електролітом Na 2 SiO 3, закон росту плівки оксиду кераміки під час процесу мікродугового окислення та вплив різного складу та концентрації електроліту на якість керамічного оксиду фільм вивчаються. Мікродугове окислення поверхні алюмінієвого сплаву є дуже складним процесом, що включає електрохімічне утворення початкової оксидної плівки та подальший розпад керамічної плівки, що включає фізичні ефекти термохімії, електрохімії, світла, електрики та тепла. .
На процес впливає сам матеріал підкладки, параметри джерела живлення та параметри електроліту, і його важко контролювати в режимі онлайн, що створює труднощі для теоретичних досліджень. Тому досі не існує теоретичної моделі, яка могла б задовільно пояснити різні експериментальні явища, а дослідження її механізму ще потребують подальшого дослідження та вдосконалення.
2 Гальваніка та хімічне покриття
Гальваніка - це нанесення шару іншого металевого покриття на поверхню алюмінію та алюмінієвого сплаву хімічними або електрохімічними методами, які можуть змінити фізичні або хімічні властивості поверхні алюмінієвого сплаву. поверхню
Провідність; покриття міддю, нікелем або оловом може покращити зварюваність алюмінієвого сплаву; і гаряче олово або сплав алюмінію з оловом можуть покращити змащувальну здатність алюмінієвого сплаву; як правило, покращують твердість поверхні та зносостійкість алюмінієвого сплаву за допомогою хромування або нікелювання; Хром або нікелювання також може покращити його оздоблення. Алюміній можна електролізувати в електроліті для утворення покриття, але покриття легко відклеїти. Щоб вирішити цю проблему, алюміній можна осадити і покрити у водному розчині, що містить сполуку цинку. Цинковий занурювальний шар призначений для перемикання алюмінію та матриці його сплаву та наступних покриттів. Важливий міст, Feng Shaobin et al. [7] дослідили застосування та механізм занурення цинку на алюмінієву підкладку, а також представили новітні технології та застосування процесу цинкового занурення. Гальваніка після занурення в цинк також може утворити тонку пористу плівку на поверхні алюмінію, а потім гальванізувати.
Безелектронне покриття відноситься до технології плівкоутворення, за якої металеве покриття наноситься на поверхню металу шляхом автокаталітичної хімічної реакції в розчині, що співіснує з сіллю металу і відновником. Серед них найбільше поширення набуло безелектронне покриття сплавом Ni-P. Порівняно з процесом гальванічного нанесення, безелектроплавне покриття є a
Завдяки дуже низьким рівням забруднення отриманий сплав Ni-P є хорошою заміною хромування. Однак існує багато технологічного обладнання для безелектричного нанесення, споживання матеріалу велике, час роботи тривалий, робочі процедури громіздкі, а якість металевих деталей важко гарантувати. Наприклад, Feng Liming et al. [8] вивчали специфікацію процесу для безелектронікельно-фосфорного покриття, що включає лише етапи попередньої обробки, такі як знежирення, занурення цинком та промивання водою на основі складу алюмінієвого сплаву 6063. Експериментальні результати показують, що процес простий, безелектронікелевий шар має високий блиск, сильну силу зчеплення, стабільний колір, щільне покриття, вміст фосфору від 10% до 12%, а твердість стану покриття може досягати більше 500HV, що набагато вище, ніж у анода. Оксидний шар [8]. Крім безелектронікального покриття сплавом Ni-P, існують інші сплави, наприклад, сплав Ni-Co-P, досліджений Янгом Ербінгом [9]. Плівка має високу коерцитивну силу, малу залишкову намагниченість і відмінне електромагнітне перетворення. Характеристики, можуть бути використані в дисках високої щільності та в інших областях, з безелектронним покриттям
Метод Ni-Co-P дозволяє отримати рівномірну товщину і плівку магнітного сплаву на будь-якій підкладці складної форми, а також має переваги економії, низького споживання енергії та зручності експлуатації.
3 Поверхневе покриття
3.1 Лазерне облицювання
В останні роки використання високоенергетичних променевих лазерів для лазерної обробки поверхонь з алюмінієвих сплавів дозволяє ефективно підвищити твердість і зносостійкість алюмінієвих і алюмінієвих сплавів. Наприклад, для нанесення плазмового покриття Ni-WC на поверхню сплаву ZA5 використовується CO 2 лазер потужністю 111 кВт. Отриманий шар лазерного плавлення має високу твердість, а його стійкість до змащування, зносу та стирання в 1.75 рази вище, ніж у напиленого покриття без лазерної обробки та в 2.83 рази від матриці зі сплаву Al-Si. Чжао Юн [11] використовував CO2-лазери в підкладках з алюмінію та алюмінієвих сплавів
Він покритий порошковим покриттям Y та Y-Al, на поверхню підкладки нанесено порошкове покриття попередньо встановленим методом порошкового покриття, лазерна ванна захищена аргоном, а також певна кількість CaF 2, LiF та MgF 2 доданий як шлакоутворюючий агент При певних параметрах процесу лазерного наплавлення можна отримати однорідне і безперервне щільне покриття з металургійною межею розділу. Lu Weixin [12] використовував CO 2 лазер для приготування порошкового покриття Al-Si, порошкового покриття Al-Si+SiC та порошкового покриття Al-Si+Al 2 O 3 на підкладку з алюмінієвого сплаву методом лазерного нанесення. , Алюмінієва бронзова порошкова фарба. Чжан Сон та ін. [13] використовував безперервний Nd:YAG лазер потужністю 2 кВт в алюмінії AA6 0 6 1
Поверхня сплаву покрита лазером керамічним порошком SiC, а модифікований шар композиту поверхневої металевої матриці (MMC) може бути виготовлений на поверхні алюмінієвого сплаву шляхом обробки лазерним плавленням.
3.2 Композитне покриття
Самозмащувальне композитне покриття з алюмінієвого сплаву з чудовими антифрикційними та зносостійкими властивостями має чудові перспективи застосування в інженерії, особливо в області передових технологій. Тому пориста глиноземна мембрана з пористою матричною структурою також привертає все більше уваги з боку людей. Увага, технологія нанесення композитних покриттів з алюмінієвого сплаву стала однією з актуальних точок дослідження. Цюй Чжицзянь [14] вивчав технологію нанесення композитних самозмащувальних покриттів з алюмінію та алюмінієвого сплаву 6063. Основним процесом є жорстке анодування алюмінію та алюмінієвого сплаву 6063, а потім використання методу гарячого занурення для введення частинок PTFE в пори оксидної плівки. А на поверхні після вакуумної прецизійної термічної обробки утворюється композитне покриття. Лі Чженьфан [15] дослідив новий процес, що поєднує нанесення лакофарбового покриття та процес гальванічного нанесення на поверхню алюмінієвих дисків, що наносяться на автомобілі. Час випробування CASS становить 66 годин, швидкість утворення пухирів ≤3%, швидкість витоку міді ≤3%, динамічний баланс зменшується на 10~20г, а смоляна фарба та металеве покриття мають гарний зовнішній вигляд.
4 Інші методи
4.1 Метод іонної імплантації
Метод іонної імплантації використовує іонні пучки високої енергії для бомбардування мішені у вакуумному стані. Можна досягти практично будь-якої іонної імплантації. Імплантовані іони нейтралізують і залишають у положенні заміщення або положенні проміжку твердого розчину для утворення незбалансованого поверхневого шару. Алюмінієвий сплав
Покращена твердість поверхні, зносостійкість і корозійна стійкість. Магнетронне розпилення чистого титану з подальшою імплантацією азоту/вуглецю PB11 може значно покращити мікротвердість модифікованої поверхні. Магнетронне розпилення в поєднанні з введенням азоту може підвищити твердість підкладки з 180HV до 281.4HV. Магнетронне розпилення в поєднанні з інжекцією вуглецю може збільшитися до 342HV [16]. Магнетронне розпилення чистого титану з подальшою імплантацією азоту/вуглецю PB11 може значно покращити мікротвердість модифікованої поверхні. Ляо Цзясюань та ін. [17] здійснили композитну імплантацію титану, азоту та вуглецю на основі плазмової іонної імплантації алюмінієвого сплаву LY12 та досягли значних ефектів модифікації. Чжан Шентао та Хуан Цзунцін з Чунцинського університету [18] провели імплантацію іонів титану на алюмінієвий сплав. Результати показали, що імплантація іонів титану на поверхню алюмінієвого сплаву є ефективним способом підвищення його стійкості до хлорид-іонної корозії, а також може покращити здатність алюмінієвого сплаву протистояти корозії хлорид-іонів. Розширити діапазон потенціалу пасивації алюмінієвого сплаву в NaCl та інших розчинах, а також зменшити щільність і розмір корозійних пор, корозійних іонами хлориду.
4.2 Рідкоземельні конверсійні покриття
Конверсійне покриття рідкоземельних поверхонь може підвищити корозійну стійкість алюмінієвих сплавів, і процес переважно хімічне занурення. Рідкоземельні елементи корисні для анодного окислення алюмінієвого сплаву. Він підвищує здатність алюмінієвого сплаву приймати поляризацію і в той же час покращує корозійну стійкість оксидної плівки. Тому рідкісні землі використовуються в
Обробка поверхні алюмінієвих сплавів має хороші перспективи розвитку [19]. Shi Tie та ін. [20] досліджували процес утворення конверсійної плівки солі церію на поверхні нержавіючого алюмінію LF21 шляхом електролітичного осадження. За допомогою ортогонального експерименту досліджено вплив суміжних факторів на процес утворення плівки та отримано найкращі технічні параметри. Результати показують, що процес анодної корозії нержавіючого алюмінію блокується після обробки електролітичним осадженням рідкоземельних конверсійної плівки, значно покращується її корозійна стійкість, а також значно покращується гідрофільність. Чжу Ліпін та ін. [21] використовували методи скануючої електронної мікроскопії (SEM), енергетичну спектроскопію (EMS) та методи випробувань сольовим розпиленням для систематичного дослідження структури, складу та компактності конверсійного покриття з алюмінієвого сплаву рідкоземельних солей церію на його корозійну стійкість. Вплив. Результати досліджень показують, що рідкоземельний елемент церію у плівці ефективно пригнічує точкову корозію алюмінієвого сплаву та значно покращує його корозійну стійкість.
Вирішальну роль відіграє стійкість до корозії. У наш час існують різні методи обробки поверхні алюмінію та алюмінієвих сплавів, і їх функціональність стає все міцнішою і міцнішою, що може задовольнити потреби алюмінію та алюмінієвих сплавів у житті, лікуванні, техніці, аерокосмічній галузі, приладобудуванні, електронних приладах, продуктах харчування та легкої промисловості та ін Потреб. У майбутньому обробка поверхні алюмінію та алюмінієвих сплавів буде простою за технологічним процесом, стабільною за якістю, масштабною, енергозберігаючою та екологічною.
Розвиток напряму. Це блок-сополімер реакції обміну ефір-амід з високою швидкістю перетворення. Коршак та ін. [11] повідомляють, що коли 1% PbO 2 або 2% PbO 2 використовується як каталізатор і нагрівається при 260 градусах протягом 3-8 годин, реакція між поліестером і поліамідом також відбуватиметься. Певний вплив на сумісність системи сумішей має реакція ефірно-амідного обміну. Xie Xiaolin, Li Ruixia та ін [12] за допомогою розчину
Певною мірою обговорювалися метод, просте механічне змішування (метод плавлення 1) і наявність реакції змішування складного ефіру та аміду (метод плавлення) для змішування ПЕТ і PA66, систематичний аналіз DSC та сумісність системи змішування PET/PA66 Sex. Результати показують, що система суміші PET/PA66 є термодинамічно несумісною системою, і сумісність суміші розплаву краща, ніж суміші розчину, а блок-сополімер, отриманий сумішшю PET/PA66, сумісний з двома. було вдосконалено; зі збільшенням вмісту РА66 температура плавлення суміші знизилася. Блок-сополімер PET/PA66, що утворюється в результаті реакції, збільшує ефект зародження PA66 на кристалізацію фази PET, що призводить до плавлення. Кристалічність французької суміші вища, ніж у суміші методом розплаву 1. Чжу Хун та ін. [13] використовували п-толуолсульфонову кислоту (TsOH) і титанатні зв’язуючі агенти як каталізатори для реакції обміну ефірами між Nylon-6 і PET для досягнення сумісності in situ сумішей Nylon-6/PET. Результати спостережень за допомогою скануючого електронного мікроскопа показують, що суміш нейлон-6/ПЕТ є кристалічною системою поділу фаз із поганою сумісністю. Додавання п-толуолсульфонової кислоти та титанатного зв’язуючого агента як каталізатора для сприяння утворенню блоків in situ. Сополімер збільшує межі розділу між двома фазами, робить дисперсну фазу очищеною та рівномірно розподіленою, а також допомагає збільшити функцію поширення тріщин у суміші . Обидва допомагають покращити сумісність суміші та підвищити міжфазну адгезію двох фаз.
2 Прогноз
За останні роки вітчизняні дослідники провели велику дослідницьку роботу над сумішами поліамід/поліестер і отримали багато корисних висновків, що заклали хорошу основу для майбутніх досліджень у цій галузі. На сьогоднішній день слід звернути увагу на сприяння подальшому розвитку сумішей поліамід/поліестерів та застосувати попередні висновки до реальної виробничої практики. Модифікуючи ці два, отримується новий матеріал, який зберігає переваги двох компонентів. Він має чудові механічні властивості, водостійкість краща, ніж поліамід, а ударна в’язкість краща, ніж поліестер. Він широко використовується в електроніці, електротехніці та автомобільній промисловості. додаток.
Посилання на цю статтю: Технологія обробки поверхні алюмінієвого сплаву
Заява про передрук: якщо немає спеціальних інструкцій, усі статті на цьому сайті оригінальні. Будь ласка, вкажіть джерело для передруку: https://www.cncmachiningptj.com/,дякую!
PTJ® забезпечує повний спектр спеціальної точності ЧПУ обробляючий Китай послуги. Сертифіковано ISO 9001: 2015 та AS-9100. Швидка точність 3, 4 та 5 осей Обробка з ЧПУ послуги, включаючи фрезерування, звернення до технічних вимог замовника, здатність обробляти деталі з металу та пластику з допуском +/- 0.005 мм. До вторинних послуг належать ЧПУ та звичайне шліфування, свердління,лиття під тиском,листовий метал та штампуванняНадання прототипів, повний цикл виробництва, технічна підтримка та повний огляд автомобільний, авіаційно-космічний, цвіль і пристосування, світлодіодне освітлення,медичний, велосипед та споживач електроніка галузей. Своєчасна доставка. Розкажіть нам трохи про бюджет вашого проекту та очікуваний час доставки. Ми з вами розробимо стратегію надання найбільш економічно вигідних послуг, які допоможуть вам досягти своєї мети. Ласкаво просимо зв’язатися з нами ( sales@pintejin.com ) безпосередньо для вашого нового проекту.
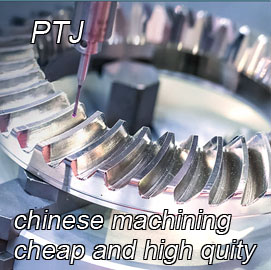
- 5 Обробка осей
- Фрезерування з ЧПУ
- Поворот cnc
- Механічна промисловість
- Процес обробки
- Обробка поверхонь
- Механічна обробка металу
- Обробка пластику
- Форма порошкової металургії
- Лиття під тиском
- Галерея запчастин
- Автозапчастини для металу
- Частини машин
- Світлодіодний радіатор
- Будівельні частини
- Мобільні частини
- Медичні частини
- Електронні частини
- Індивідуальна обробка
- частини велосипедів
- Обробка алюмінію
- Обробка титану
- Механічна обробка нержавіючої сталі
- Обробка міді
- Латунна обробка
- Суперсплавна обробка
- Загляньте в обробку
- Обробка УВМВ
- Однорідна механічна обробка
- Обробка PA6
- Обробка PPS
- Обробка тефлоном
- Механічна обробка інконеля
- Обробка інструментальної сталі
- Більше матеріалу